Corrosion Resistant Coatings
Anti-Corrosion Coatings
Combat Corrosion with Protective Treatments
Corrosion can compromise the integrity and performance of metal components over time, especially in demanding environments. Lutco offers a variety of anti-corrosion coating options to help customers extend part life and durability.
Our engineers work with you to identify the most effective, cost-efficient solution based on your application’s environment, material, and performance requirements.
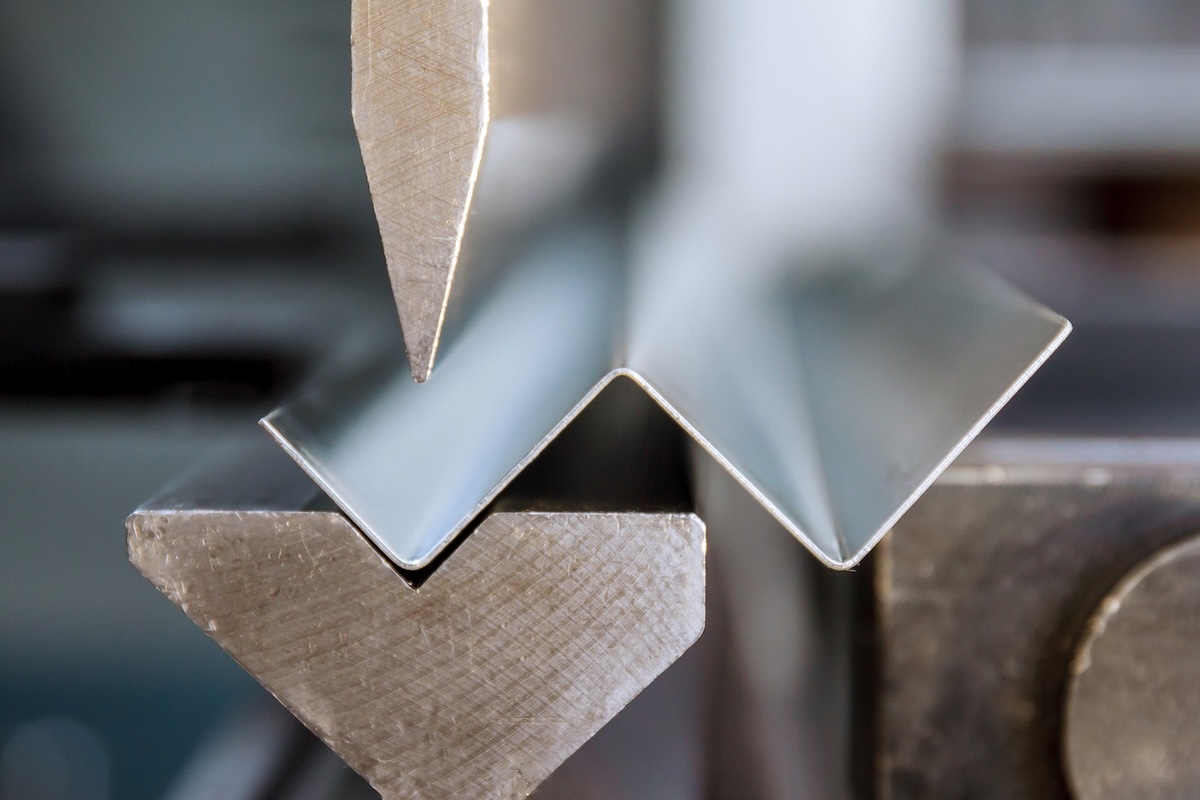
Zinc Plating
(per ASTM B633)
DÖRKEN ZINC
Flake Coating
AG 3000
(ArmorGalv® Thermal Diffusion Coating)
Compare Coating Options
Coating Type | Salt Spray Resistance | Coating Thickness | Typical Applications |
Zinc Plating (per ASTM B633) | 144 hours (min) | .0002”–.0006” | Agricultural and industrial parts with light exposure to the elements |
DÖRKEN ZINC Flake | 960–1,000 hours | .0004”–.001” | Agricultural, transportation, and industrial components exposed to corrosive environments |
AG 3000 (ArmorGalv®) | 3,000 hours (min) | .001″-.002″ | Marine, mining, industrial, and heavy outdoor machinery in extreme conditions |
Note: Salt spray testing (ASTM B117) simulates long-term environmental exposure. Lutco will help determine the most appropriate option based on your part’s intended operating conditions.
Zinc Plating
(per ASTM B633)
Zinc plating is a cost-effective method of corrosion protection that applies a thin sacrificial zinc layer to steel components. The zinc coating corrodes preferentially, protecting the underlying steel. Lutco’s zinc plating complies with ASTM B633 standards and is ideal for light-duty applications where moderate corrosion resistance is sufficient.
- Salt Spray Resistance: ≥ 144 hours (ASTM B117)
- Coating Thickness: .0002″–.0006″
- Substrate Compatibility: All steel substrates
- Compliance: RoHS and REACH compliant (Type V – Clear Blue)
Ideal Applications
- Agricultural and industrial equipment components with intermittent or low exposure to moisture
- Indoor mechanical assemblies and brackets
- Sheet metal enclosures or housings in protected environments
Key Benefits
- Economical protection for steel components
- Good adhesion and uniform coverage
- Suitable for chromate conversion post-treatment for added resistance and appearance
- Compatible with high-volume manufacturing and plating lines
DÖRKEN ZINC
Flake Coating
This non-electrolytic zinc flake coating provides superior cathodic protection and barrier performance for steel components. It is often selected for its hydrogen embrittlement-free application process, consistent torque/tension behavior, and resistance to mechanical and chemical wear.
- Salt Spray Resistance: ≥ 960–1,000 hours (ASTM B117)
- Coating Thickness: .0004″–.001″
- Substrate Compatibility: All steel substrates
- Compliance: RoHS and REACH compliant
Ideal Applications
- Agricultural equipment exposed to long-term outdoor conditions
- Transportation and utility components exposed to deicing salts and chemicals
- Applications where electrical conductivity and grounding are critical
- Ball transfers for cargo handling systems
Key Benefits
- No hydrogen embrittlement risk
- Uniform coating thickness across complex geometries
- Excellent resistance to temperature variation and chemical exposure
- Proven performance in automotive, rail, and heavy equipment industries
- Compatible with dip-spin and spray coating processes for batch production
AG 3000
(ArmorGalv® Thermal Diffusion Coating)
AG 3000 is a premium thermal diffusion zinc alloy coating that forms an intermetallic bond with the substrate. Known for its exceptional corrosion resistance, this coating is especially effective in marine, mining, and chemically aggressive environments, where long-term protection is critical.
- Salt Spray Resistance: ≥ 3,000 hours (ASTM B117)
- Coating Thickness: .001″-.002″
- Substrate Compatibility: All steel substrates
- Compliance: RoHS and REACH compliant
Ideal Applications
- Marine components and coastal infrastructure hardware
- Mining, oil & gas, and off-road industrial equipment
- High-abrasion parts requiring durable coating adhesion
- Environments with frequent wet/dry cycles and salt exposure
Key Benefits
- Exceptional protection in extreme environments
- Coating is metallurgically bonded to steel surface—no flaking or peeling
- Tolerant of thermal cycling, abrasion, and mechanical stress
- Compatible with additional sealants or topcoats for enhanced wear or chemical resistance
- Low maintenance, long-life solution for mission-critical assemblies
Smarter Protection Without Overdesign
Many applications don’t require the added cost of stainless steel to meet corrosion resistance goals. Lutco works with customers to assess environmental risk and recommend the right coating for performance, cost, and manufacturability.
Whether you’re facing extreme conditions or simply want to enhance part longevity, we’ll help you choose the right protection for the job.
Why Anti-Corrosion Coatings Matter
Protecting metal components from corrosion is essential for ensuring long-term performance, minimizing maintenance, and avoiding costly equipment failures. Lutco offers a range of anti-corrosion coating options to meet the diverse needs of our customers across industries—from agricultural machinery to fluid control systems and outdoor equipment.
Environmental exposure to moisture, oxygen, chemicals, or salt can cause rust, surface degradation, or structural failure over time. Choosing the right anti-corrosion coating extends the lifespan of your parts and assemblies while reducing the need for more expensive materials like stainless steel.
Our engineers help customers select the most cost-effective solution based on:
- Environmental exposure (e.g., saltwater, humidity, temperature extremes)
- Part function and location
- Material type
- Target service life and budget
Get a Quote for Corrosion-Resistant Components & Assemblies
Let us know your operating environment and part requirements—we’ll come through with a corrosion-resistant solution that meets your needs.
Contact us to find out why leading OEMs rely on Lutco!